10 Ways to Create a Culture of Continuous Improvement in Operations
Discover the transformative strategies for cultivating a culture of continuous improvement in operations, distilled from the expertise of industry leaders. This article unveils practical insights across a spectrum of innovative topics, from AI-driven optimization to dynamic cross-functional sprints. Engage with the knowledge of seasoned professionals to elevate operational excellence and drive sustainable growth.
- Empower Teams with AI-Powered Process Optimization
- Foster Innovation Through Decentralized Decision-Making
- Implement 'Lessons Captured' for Continuous Improvement
- Track Progress with Real-Time Project Management
- Launch Process Improvement Challenges for Team Engagement
- Embed Feedback Loops in Quarterly Innovation Labs
- Encourage Experimentation with Mixed-Team Innovation Labs
- Develop Structured Training for Efficiency and Expertise
- Run Cross-Functional Innovation Sprints Regularly
- Host Monthly Process Reviews for Team-Driven Solutions
Empower Teams with AI-Powered Process Optimization
Creating a Culture of Continuous Improvement Within the Operations Team
In IT, fostering a culture of continuous improvement is essential to efficiency and innovation. As an IT Director, I ensure operations teams evolve to meet challenges and optimize processes. A culture of improvement thrives when feedback, learning, and process optimization are embedded in daily operations.
We emphasize collaboration, transparency, and empowerment. Involving team members in decision-making promotes ownership. Cross-functional collaboration enhances innovation, allowing teams to share insights and best practices for process optimization.
Specific Initiative: AI-Powered Process Optimization
We've implemented AI-powered tools for process optimization. These tools assist with static code analysis, vulnerability scanning, and fraud prevention, continuously improving. Integrating AI coding models with SonarQube helps identify vulnerabilities early, ensuring high-quality code.
AI also identifies operational inefficiencies, uncovering bottlenecks, automating tasks, and reducing errors, which improves efficiency and security.
Encouraging Innovation Through Regular Feedback
Innovation thrives through feedback. We collect feedback on processes and user experiences using tools like Hotjar and LogRocket. These insights help refine workflows and user interfaces.
Additionally, we hold brainstorming sessions and retrospectives where team members propose ideas, challenge processes, and experiment with tools. This collaborative environment fosters innovation and empowers everyone to contribute.
Recommendations for Fostering Continuous Improvement:
1. Empower Teams - Involve team members in decisions and encourage ownership.
2. Leverage AI - Use AI tools to automate tasks and optimize workflows.
3. Encourage Cross-Functional Collaboration - Share ideas and best practices across teams.
4. Continuous Feedback Loop - Collect feedback to optimize processes.
5. Create a Safe Space for Innovation - Foster experimentation through brainstorming.
Building a culture of continuous improvement requires an environment where innovation is encouraged, learning is constant, and team members contribute to process optimization, laying the foundation for success.
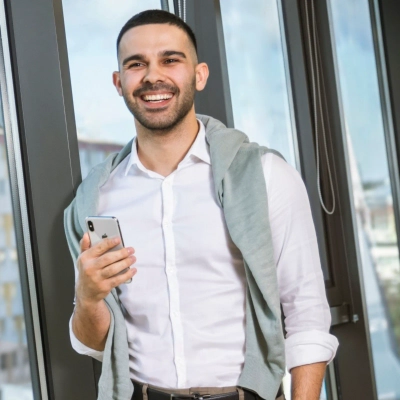
Foster Innovation Through Decentralized Decision-Making
Fostering innovation in management and cultivating a culture of continuous improvement are integral to driving meaningful change in healthcare IT. At our organization, we've adopted a multi-faceted approach, combining empowered leadership, structured processes, and a commitment to experimentation.
One example is our decentralized decision-making model, where team leads are empowered to pilot new ideas. For instance, a team used their insights to develop a real-time patient engagement dashboard, reducing no-show rates by 30%. This approach not only encourages ownership but also accelerates the development of impactful solutions.
We embed continuous improvement through frameworks like Lean and Plan-Do-Check-Act (PDCA). Weekly retrospectives help identify bottlenecks and refine workflows incrementally. This method, inspired by a healthcare IT provider's success in streamlining API integration processes, has significantly improved efficiency while fostering a mindset of progress over perfection.
Experimentation is core to our innovation culture. Through an innovation lab, employees dedicate 10% of their time to passion projects aligned with organizational goals. This led to the development of a chatbot that improved patient query resolution rates by 40%. By creating a safe environment where failure is celebrated as learning, we encourage bold thinking.
We emphasize data-driven decision-making and cross-functional collaboration. Using AI-powered analytics, we've optimized processes like scheduling and interoperability, aligning with industry shifts toward value-based care.
These strategies ensure our organization remains agile, forward-thinking, and deeply committed to delivering impactful solutions in a rapidly evolving healthcare landscape.
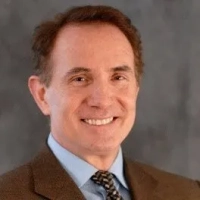
Implement 'Lessons Captured' for Continuous Improvement
We've implemented a "Lessons Captured" program where crews document one improvement opportunity after every project. Unlike traditional post-mortems that focus on problems, crews identify one thing they'd do differently next time, regardless of how well the job went. These insights are shared in monthly team huddles where the best ideas receive implementation funding. This approach normalized constructive feedback and created healthy competition for innovation. One apprentice's suggestion for modified flashing techniques on Spanish tile roofs reduced our installation time by 22% and has become our standard practice. Making improvement everyone's responsibility, not just management's, transformed our culture.
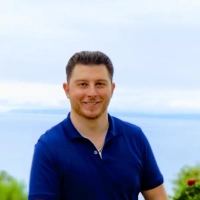
Track Progress with Real-Time Project Management
When it comes to fostering innovation in a business like ours, it's all about creating an environment where new ideas are welcomed, and employees feel empowered to contribute. Over the years, I've focused on continuous improvement through a mix of technology, employee development, and a commitment to open communication.
One example that stands out is how we implemented a project management software that allowed our teams to track the progress of every job in real time. This software wasn't just for keeping tabs on deadlines, it also gave us deeper insights into how we could optimize our workflows. For instance, by using the software, we identified that certain projects had a 20% longer turnaround time than others. We dug deeper and found that the issue was with supply chain management, so we introduced new ordering protocols, reducing delays by 15%.
In addition to tech, we hold monthly innovation meetings with our team. Everyone, from project managers to field workers, can suggest new tools, techniques, or processes they think might improve our work. By involving everyone, we foster a culture where each person feels they can make a real difference in how we operate.
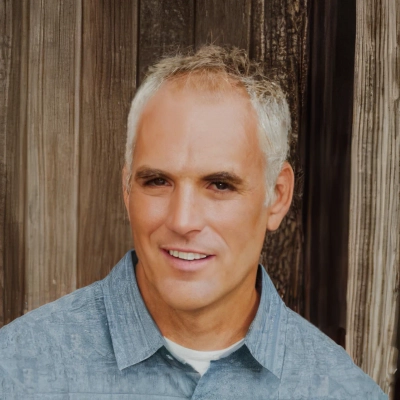
Launch Process Improvement Challenges for Team Engagement
To foster a culture of continuous innovation within our operations team, we focus on open communication and actively seek input from all team members. We encourage them to share their ideas for improving workflows, eliminating inefficiencies, and boosting overall productivity. Regular feedback loops are essential, whether through meetings or suggestion boxes where everyone feels their input is valued.
One initiative we've implemented is a process improvement challenge, where team members can propose ideas for enhancing specific areas of operations. The best ideas are rewarded and given the opportunity to be tested and implemented. This has not only led to several impactful changes but also created a sense of ownership and engagement within the team. By involving everyone in the process, we continuously refine our operations and adapt to new challenges!
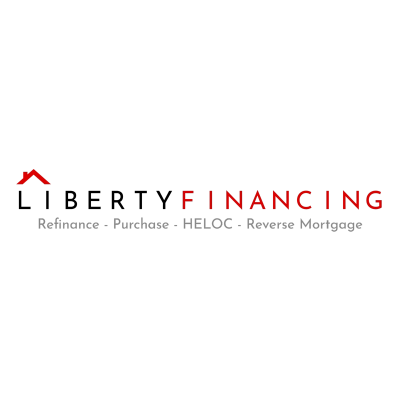
Embed Feedback Loops in Quarterly Innovation Labs
We created a culture of continuous improvement by embedding feedback loops and rewarding proactive problem-solving within our operations team. One specific initiative was launching a "process challenge" where team members pitch and test efficiency ideas each quarter. In addition, we provided time and resources to implement the best suggestions, tracking their impact. This approach empowered ownership and creativity. Ultimately, it fostered innovation, improved workflows, and strengthened team engagement around shared operational excellence.
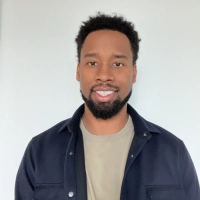
Encourage Experimentation with Mixed-Team Innovation Labs
We have learned that creating an environment where employees feel empowered to experiment and fail fast is key to sustainable innovation.
One example is our quarterly "Innovation Labs," where mixed teams of experienced formation specialists, support staff, and marketing experts spend two days testing fresh ideas for client onboarding processes. For instance, a recent Lab introduced a new digital pre-check tool that halved our document turnaround time. We also use regular feedback surveys to gather front-line insights, which guide our management in setting clear objectives for the next quarter. This results in a continuous improvement loop where staff see their input turned into practical actions.
We back these initiatives with transparency and open communication. During monthly roundtable sessions, management shares progress metrics, such as client satisfaction scores and error rates, to keep everyone focused on measurable targets. Besides fostering accountability, this approach helps our team identify trends and propose new solutions quickly. The outcome is an energetic and adaptable culture that encourages everyone to think creatively.
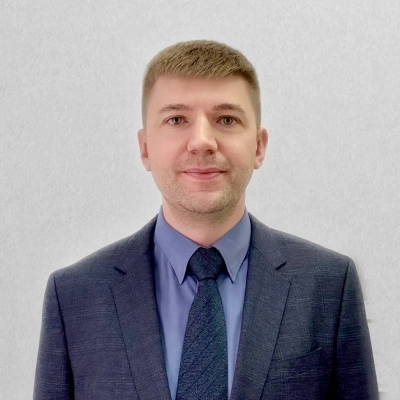
Develop Structured Training for Efficiency and Expertise
Creating a culture of continuous improvement within my operations team starts with leading by example and fostering an environment where feedback and innovation are valued. With over 15 years of experience in gardening, landscaping, and lawn care, I have seen firsthand how small process improvements can lead to significant long-term gains. One specific initiative I implemented was a structured training and development program for my team, focusing on both horticultural expertise and efficiency in service delivery. By leveraging my certification in horticulture, I designed workshops that not only improved our technical skills but also encouraged team members to identify inefficiencies in their daily tasks. This empowered them to suggest new techniques and tools, leading to faster job completion without sacrificing quality. The result was a more engaged team that felt ownership over their work and consistently sought better ways to serve our clients.
A standout success from this initiative was streamlining our garden maintenance process by introducing a customized digital job-tracking system. My experience in managing over 700 gardening and landscaping projects helped me recognize that time management and task coordination were key to improving efficiency. By integrating a system where team members could log tasks, track progress, and communicate in real time, we reduced time wasted on redundant efforts and improved accountability. This system not only improved productivity but also enhanced customer satisfaction by ensuring no details were overlooked. Thanks to my deep understanding of both practical and theoretical aspects of horticulture, I was able to refine this system based on real-world needs, making it an invaluable tool for our team's continuous improvement.
Run Cross-Functional Innovation Sprints Regularly
One example from our business is how we run regular innovation sprints. Every few months, we pull together cross-functional teams to tackle a specific challenge—say, improving our customer feedback loop—and spend a few days brainstorming, prototyping, and testing new ideas. This collaborative process generates creative solutions and also breaks down silos between departments, encouraging everyone to contribute. One sprint led us to integrate a customer survey tool directly with our project management system, which sped up our product iterations and improved our response times.
We also foster a culture of continuous improvement by keeping feedback channels wide open. Monthly all-hands meetings, informal idea-sharing sessions, and ongoing learning opportunities are all part of our routine. We invest in in-house workshops and online courses, and we occasionally invite industry experts to challenge our thinking. The key is creating an environment where experimentation is encouraged and mistakes are seen as learning opportunities, which has been a major driver in keeping our processes agile and our team motivated.
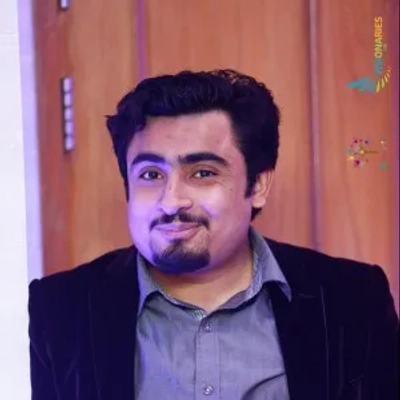
Host Monthly Process Reviews for Team-Driven Solutions
I create a culture of continuous improvement by encouraging open feedback and giving my team the tools they need to succeed. One specific initiative I've implemented is a monthly process review meeting, where team members share ideas on how to improve efficiency. We analyze workflows, identify bottlenecks, and test new solutions. For example, after noticing delays in order processing, we streamlined communication between departments using a shared digital tracking system, which cut processing time by 30%. Empowering the team to contribute ideas keeps everyone engaged and focused on innovation.
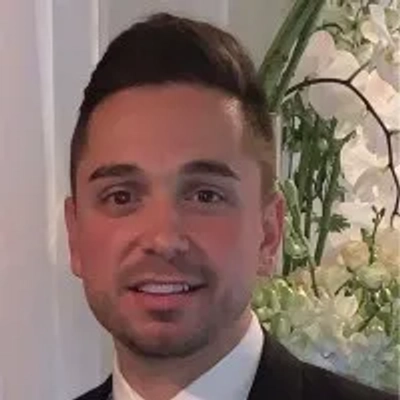